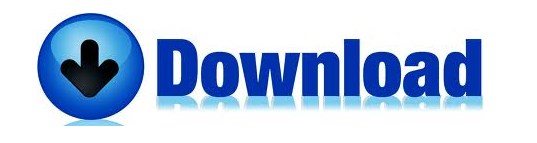
With feedback obtained from customers, consumers, patients and other stakeholders, an organization could consider to change the design of a medical device or certain processes, e.g. The information gathered in the feedback process shall serve as potential input into risk management for monitoring and maintaining the product requirements as well as the product realization or improvement processes.
#Risk management iso 13485 verification#
The extent of verification activities shall be based on the supplier evaluation results and proportionate to the risks associated with the purchased product.įMEA can also be used to identify areas of significant risk at suppliers that demand special attention.Ĭlause 8 – Measurement, Analysis and Improvement Non-fulfilment of purchasing requirements shall be addressed with the supplier proportionate to the risk associated with the purchased product and compliance with applicable regulatory requirements. The criteria shall be proportionate to the risk associated with the medical device. The organization shall establish criteria for the evaluation and selection of suppliers. to ensure that design input requirements can be verified or validated. to clarify product usability and safety requirements.
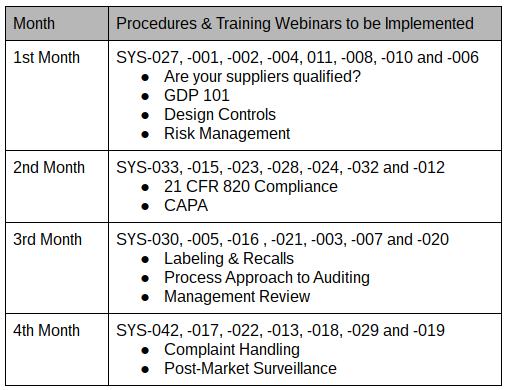
New requirements for risk management outputs: Consideration should specifically be given to what could be the consequences if employees interpret the essence of a certain training incorrectly and what the subsequent impact could be on a product’s quality. The risks should be considered if the given training is not fully understood. The methodology used to check effectiveness of a training is proportionate to the risk associated with the work for which the training or other action is being provided. The controls shall be proportionate to the risk involved and the ability of the external party to meet the requirements in accordance with 7.4. The organization shall retain responsibility of conformity to this International Standard and to customer and applicable regulatory requirements for outsourced processes. When the organization chooses to outsource any process that affects product conformity to requirements, it shall monitor and ensure control over such processes.

The revised ISO 13485 standard requires medical device companies to make risk-based decisions related to purchasing and product realization activities and other aspects of the quality management system, such as training. ISO 13485:2016 section 4.2.1 states, “The organization shall apply a risk-based approach to the control of the appropriate processes needed for the quality management system.” In other words, anything that affects the quality system needs to be viewed from that risk perspective. While ISO 13485:2003 mainly applied risk management for activities related to product realization with a primary focus on the design and development of medical devices, the revised ISO 13485:2016 expands risk management to include processes such as purchasing and training. Risk Management is an intrinsic concept within Medical Device regulations. The current MDD as amended references the term risk more than 50 times.

The term “risk” is referenced over 15 times in the revised Quality Management Standard (QMS) ISO 13485:2016.
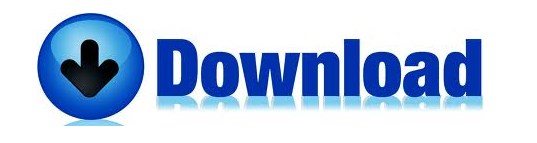